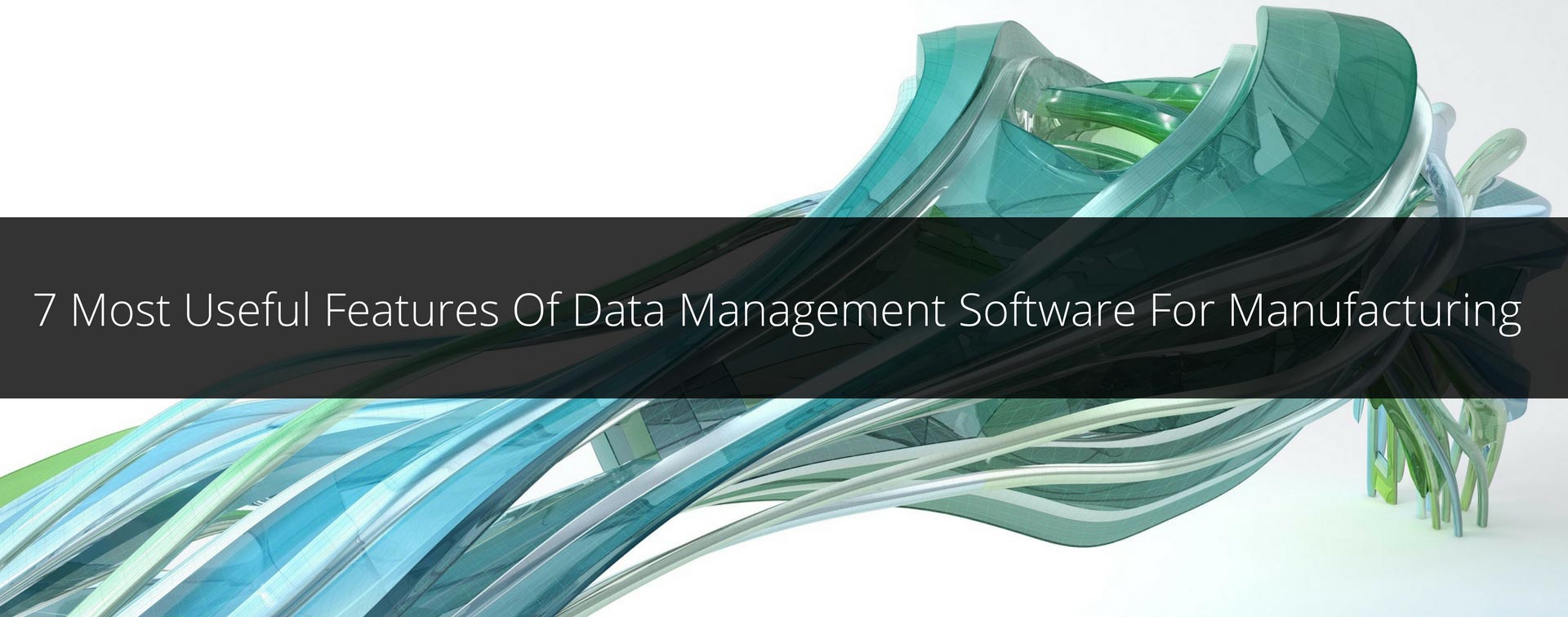
Design and engineering in the manufacturing industry are becoming more complex while the pressure to meet tight deadlines has increased.
The processes are involving more specialists who need to work on a file simultaneously and more stakeholders who need to review and comment on the designs.
To streamline workflow, manage product data, reduce error, and ensure seamless collaboration, manufacturers are using advanced software applications to manage product data and version control.
What’s a Product Data Management Software Application?
It facilitates collaboration among designers, engineers, and stakeholders so projects can be structured and managed efficiently.
Product information can be consolidated and stored so teams can reuse data without having to re-create designs from scratch.
The design files will not only be used in the manufacturing process but also for simulation purposes to validate and optimize a design.
When selecting Product Data Management software, consider these features, which are often used in the manufacturing industry:
1. Shared Views
What's-a-Vault-Software-Application.jpg?width=750&name=1)What's-a-Vault-Software-Application.jpg)
Designers can publish a visual representation of a design and specify the aspects that require feedback to help focus the comments while reviewers can access the shared view on any browser and see the design from every angle.
In addition, managers can have quick access to all the shared views and see comments from various stakeholders all in one place.
2. Direct CAD Integration
When you work with partners, vendors, and customers who use different design software applications, the collaboration process can be hindered by the variation in file formats that aren’t always compatible with each other.
To ensure seamless collaboration, you need a solution that gives you the ability to manage third-party data natively to bypass any translation.
With direct CAD integration, you can work with anyone from anywhere regardless of what software they use.
3. Data Reuse
Data-Reuse.jpg?width=750&name=2)Data-Reuse.jpg)
This feature allows designers to reuse whole or part of an existing design and maintain all existing references while helping manufacturers maximize ROI on design data by driving design reuse.
4. Concurrent Design
This vital data management feature enhances productivity and controls access to design data by allowing different parties to work on the same design file concurrently without risking overrunning one other.
Workgroups can balance resources and finish projects quicker with seamless design communications.
Since designers are able to see each other’s changes as they happen, they can react and respond accordingly to avoid errors.
5. Revision Control
It also enables managers to audit and track revision history of the design files from one single location.
This feature helps reduce version control errors by securely releasing and tracking the files through the design cycle and making sure that team members only access the correct version of data.
6. Automated Change Order Workflow
A robust change control workflow feature can automatically reference the preliminary design and related documentation as soon as you enter the details of a change order.
From there, you can capture progress and record additional comments to efficiently and effectively manage change orders.
Stakeholders are assigned responsibility for processing the change order based on configurable routings.
Notifications are sent, comments are recorded, progress is monitored, and reports generated to keep the project moving along while helping design teams avoid costly mistakes and remove bottlenecks.
7. Search Functionality
Search-Functionality.jpg?width=750&name=4)Search-Functionality.jpg)
A robust search feature supports file content indexing, which allows designers to search for text and phrases inside documents, including MS Office files and design documents.
Since many design files involve thousands of parts, it’s also important that all links to parts and assemblies are updated as they’re renamed or removed in order to save time and reduce errors.
Choosing a Product Data Management Software for Manufacturing
To support your manufacturing and simulation processes, you need a robust data software application with the key features mentioned above.
Hagerman & Company works with 3 systems that offer a customized approach to helping companies solve data management challenges and assist with implementation and documentation.
Request more info to see how we can assist you.
Comments